At AlienGen we love to design and implement innovative solutions that work for people. We get really excited when a design problem comes at the intersection of complex offline or physical processes and business goals of transparency and process analysis.
Our mission is always to enhance and augment workflows to ensure happiness, safety and efficiency. We believe these 3 factors are not incompatible if you have the right tools to make your employees work on what matters.
About Baosteel
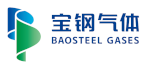
After more than 30 years of growth, Baosteel has become China's most competitive iron and steel enterprise. In 2012, the company made its way into the Fortune Global 500 for the ninth consecutive time, ranking at 197. Beyond its core steel production business, Baosteel operates a portfolio of supporting businesses including gases and industrial chemical products. By the end of 2011, Baosteel had a total of 116,702 employees scattered around the world.
Challenge
Baosteel’s gases subsidiary has several physical processing and filling facilities around Greater China. These facilities’ core operations include producing gases like Nitrogen, Oxygen, Hydrogen or Argon and filling cylinders used to store and distribute the gases across China. At the time of engaging AlienGen, all records and operations of Baosteel’s supply chain, maintenance and filling process was tracked through paper-based reports, which were then manually processed and aggregated to be input into a Salesforce based ordering system.
Baosteel needed a complete platform to track the situation in real-time, detect any anomalies, plan cylinder maintenance to maximise availability, and ensure the safety of the supply chain processes. Given Baosteel’s lack of any existing digitized solution, the entire supply chain tracking ecosystem required engineering, from the front-end software platform to the embedded devices and tracking technology that would drive the monitoring and analysis process.
Solution
AlienGen’s developed a two-tier digitalization strategy to Baosteel’s core problem of slow, error-prone reporting.
At the business logic level, we created a centralised web platform to retrieve and aggregate all the events from the different touchpoints on-site at facilities, which was then able to generate reports for finance by integrating with their existing Salesforce ordering management.
At systems infrastructure level, we worked with a hardware partner to create a network of terminals at different locations of a facility: filling lines, cylinder maintenance rooms, and offices. Using IoT embedded devices equipped with RFID scanners, every time a cylinder with an RFID tag is used at the different terminals, we’re able to send events to the web platform and print reports for the facility management teams.
In addition to fixed-position terminals, we implemented a flexible mobile solution for a handheld RFID reader linked with a wearable bluetooth printer that could be deployed to drivers in the transport fleet, completing the loop between facilities management and distribution.
Aggregating and combining all of the data generated from terminals and readers, Baosteel was empowered to track the proper execution of all the processes across the entire division, and gain close to real-time updates by removing the time used to generate and reconcile reports on paper.
For AlienGen, we also take pride in the frictionless integration of a technology solution that brings real value to the business while removing busy work from team members’ daily jobs-to-be-done, allowing them to concentrate on the real work of producing, storing, and distributing resources.